It doesn’t happen too often in the music gear world that a new company emerges with some truly unparalleled designs, even more rare that that originality remains consistent with each new product announcement. Latvian brand Gamechanger Audio is an example of such, and it truly lives up to its ambitious name. We sat down with the GCA founder Ilja Krumins to talk about the origins of the company, his vision and philosophy, inspirations, future plans, and more.
Origins
Eldar Tagi: Hi Ilja. Thank you for taking the time to talk to us. Let’s start at the very beginning, as I’m sure many of our customers would love to know the backstory behind the Gamechanger. Did you always plan to be an instrument designer? How did you come onto this path? Who is Gamechanger Audio today?
Ilja Krumins: To be fair the plan has always been to create something in the realm of music. First I thought it was going to be purely in the form of songs and albums, but turns out building music products and instruments is also a very deep form of creative expression.
Me and the other engineers/co-founders are all lifelong Rockabilly, Psychobilly, and Rock'n'Roll musicians. I've played in various rockabilly bands professionally for many years. That was a really cool life but I've also always felt a deep connection to exact sciences and technical things. Even though music is really cool but it's a very abstract lifestyle…Especially when creating original material.
All of that work that goes into composing songs and making recordings just ends up being an MP3 file or a CD in someone's car. So in the last years of music college (ICMP in London) I started experimenting with building guitar and recording-related tech projects. My biggest project took a year to complete—it was an automatic Bigsby tremolo arm that vibrates on its own (driven by a motor). The result was this fantastically uncomfortable contraption that produced amazing vibrato effects on my Gretsch but that's about it - it was clear to me that what I've built something really special, but that it has no potential to become a commercial product. Still, I felt like I learned a lot and new ideas started coming—including the idea for the PLUS Pedal. I knew there was a huge amount of potential for a pedal like that—real piano-style sustain for all instruments?? Woooow! Yet it was clear to me that I would need a team of serious engineers to build the PLUS Pedal.
One day I was talking to a fellow musician about my idea and he seemed very intrigued - I had known Kristaps only as a Kick-Ass rockabilly double-bass player, but turned out that music was just his hobby—his real job was as an electronics engineer. So we sat down then and there, discussed everything that we would need to do to build a prototype for the PLUS Pedal, shook hands, and pretty much started working the next week. He also enlisted his best friend and bandmate Martins, who (besides being a young Mark Knopfler's doppelganger) is an extremely skilled and experienced electronics engineer and circuit board designer. For the first year, we worked evenings at my house + weekends, and then when we finally felt that we had something close to a prototype, we enlisted the help of my former school buddy Didzis. Didzis was the first guy from my circle of friends who went to business college and started wearing a suit over his Metallica tattoos, working in a corporate environment. When Didzis was on board we felt like we had the necessary combined knowledge to start a Music Electronics Company.
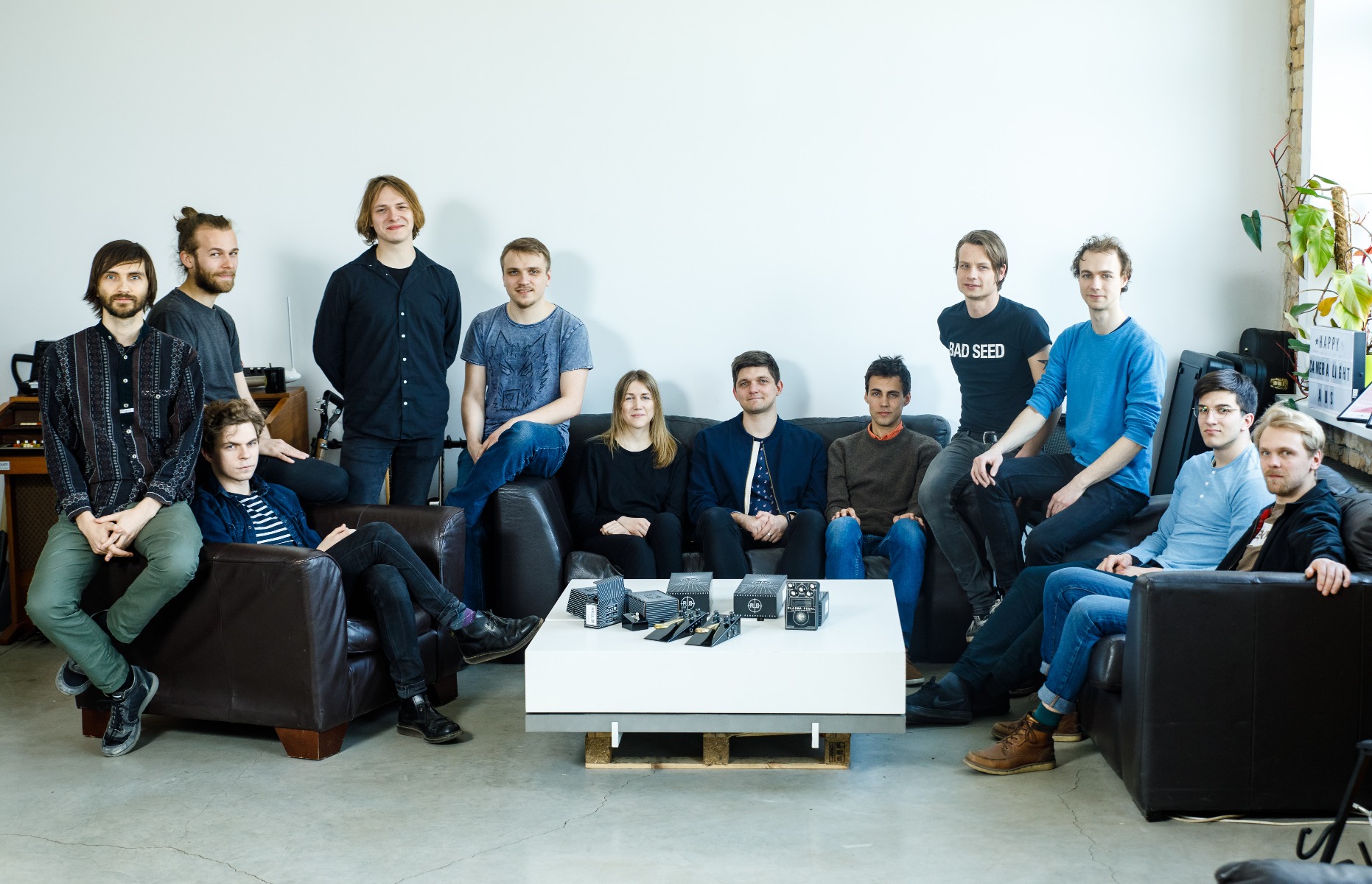
ET: I suppose, like in many other places, the music scene in Latvia changed over the last couple of decades. Can you describe this change? How has the local scene affected what you do as an instrument designer?
IK: Latvia is a strange place - we have very strong traditions in classical and jazz education so there's always a lot of young Jazz freaks around. Also we have extremely cold depressive Winters so there's also a lot of scary metal.
The current trend seems to be electronic music - we have a lot of kids who do modular synth stuff and do insane rave-parties—I'm pretty sure Erica Synths is responsible for that, ha ha.
Me and the engineers—we've always been in love with American genres such as Blues, Folk, Bluegrass, Country Rockabilly, Rock and Roll, so we've done what we can to create a scene here. We're also into heavy stuff and German techno :O
Dreams Coming True
ET: Who and what do you consider to be the major influences on your vision personally, and on the overall direction of Gamechanger Audio?
IK: Well, to be honest, I think most guitar gear is kind of boring. I am really inspired by the big important Musical inventions that helped shape and Define the sounds of whole genres. For example, without the DigiTech Whammy, there would have been no White Stripes or Rage Against the Machine. Now that is some bold thinking, especially for those times and I find that really inspiring—if you're going to build something then why not use your freakin' imagination, you know?
In broader terms, I see each of our products as a functional art project, or perhaps - Gamechanger Audio is like a band of engineers and each new release is the “New Album”.
Our goal is to keep consistently producing beautiful, artistic pieces of music-technology for many years to come—each one with its own soul and character.
In purely artistic terms, I draw a lot of inspiration from filmmakers David Lynch (imagination, depth) and Quentin Tarantino (style, balls), because they both are epitomes of originality, creative vision AND commercial success.
ET: What was it like for you to collaborate with Third Man Records on that limited edition Plasma Coil pedal? Did the idea come from them originally?
IK: It definitely was a dream come true for us. When we built the PLASMA Pedal it was clear to me that someone like Jack would appreciate the sound and the aesthetic, so we just kind of jokingly called it the Jack White sound. Then a year later he actually reached out to US. Wow! We met and discussed adding some new features and then it was another 4-5 months of development and design work together with the amazing Third Man Records team.
Still, I think that the real hero here is our engineer Martin—he really concocted something insane with these unique octave circuits. The PLASMA Coil is just ridiculously aggressive and heavy. I LOVE how great it sounds on guitar..
ET: To me, the interesting part about Gamechanger is that it seems to be more about technology, and vision rather than format. Thus you are gaining visibility in the guitar player world, synth world, and even the pro audio world (the Plasma drive was released in all of these configurations)...markets which do not always feature a lot of crossover. Was that an intentional strategic route for you, or did things just evolve naturally this way?
IK: I think it's kind of strange that most gear companies box themselves in so strictly. Music is changing and the lines between guitars, synths, laptops, plugins, and pedals are getting more and more blurred. So who said you need to just be a Pedal company - at the end of the day all you're doing is making tools for musicians. You should feel free to explore all formats and platforms if the idea calls for it.
For us an original idea is what matters most. There's a lot of brainstorming involved and we set strict standards for ourselves, so most new product ideas get discarded. When we do have the “Eureka” moment—then we just focus on building it and making it the best possible version of the idea. For example, the MOTOR Synth made more sense as a Standalone instrument, not as a guitar pedal. Teenage Engineering are an awesome example of this kind of thinking and they are a big inspiration!
The MOTOR Synth
ET: Let’s talk about the Motor Synth. We are very excited about this release in particular. Can you tell us what the Motor Synth is? Where did the idea come from, and what challenges did you encounter when realizing it?
IK: The Motor Synth is an electromechanical synthesizer that uses electromotors instead of traditional VCOs as the sound source. When you think about it—an electromotor is also a voltage controlled oscillator. The seed for this idea came from our head engineer Martin's imagination—one day he showed up at work saying he had some kind of fucked up dream about drills and guitars. So naturally, our first thought was, “Fuck—yeah let's put a MOTOR into a pedal! Let's call it MOTOR Pedal!”
When we started weighing out the possible challenges we realized that there are two huge problems with a guitar pedal like that.
Number one would be pitch tracking - something that still hasn't really been solved perfectly in the pedal industry. An Electric guitar produces a pretty messy output and if you want to create a polyphonic pitch-tracking system there is a lot of processing power involved, as well as very complex software.
The Second challenge would be developing very responsive and very stable Motor drivers (micro-controllers). We looked at the available solutions from the Drone industry and realized that a lot of the groundwork is done, but still, the requirements for a musical instrument would be even higher than the most advanced Drone-motor drivers.
So we decided to focus on an instrument that wouldn't require pitch tracking - something like a piano or something with buttons, where at least the note values would have been set. That way we just needed to solve the Motor driver situation.
What we did is we hired a very talented engineer who had just finished a five-year run at a 3D printer company. 3D printers also require super-precise control over electromotors and this guy Valters (Valters Celmiņš) was the top expert in our region. Turns out he also plays a little bit of keys is a really awesome guy. It took Valters a little over a year to develop what we think is the most advanced, precise and stable Motor driver on the market today (we're thinking about launching it in the Drone racing world). Meanwhile, me, Kristaps and Martins were designing the MOTOR Synth: layout, controls, functionality, filters and all the other details.
The end result is absolutely amazing and even though it has been a gigantic technical challenge, and there were times where we literally thought we have lost our minds, I think in the end we've achieved something very important here. Just as the PLASMA pedal the MOTOR Synth is a truly analogue instrument and the sounds it produces cannot be replicated with plugins or other synths. It is truly a unique instrument and every session with the MOTOR Synth turns into an inspiring and deeply immersive experience.
ET: As far as I understand different waveforms are derived using different means of extracting sound from the motors, like electromagnetic induction and IR sensing technology? Can you please explain this in more detail for our readers?
IK: The MOTOR Synth captures the electromotors' sound in two ways - the first one is by using electromagnetic inductors placed next to the motors. You can think of them as tiny guitar pickups - as the Coils inside the Motor spin, they generate impulses in the magnetic field. These impulses can be picked up with an inductor and turned into audio signal.
Secondly, there are specially-designed reflective discs attached to the motor's spinning shaft. Each of these discs holds three standard waveforms printed circularly onto their surface, and there are three corresponding optical sensors designed to read those spinning patterns. The three patterns are Sine, Square and Sawtooth, each with a dedicated optical sensor and with 7 periods per 1 revolution (to match the number of Coil-pairs inside the Motors). In theory, you could print any other waveshape on the discs, but we simply chose the 3 fundamental ones as a good, well-rounded combo. In reality, the quirks and imperfections of the optical sensor and disc system make a big impact on the resulting output—those can not really be called pure waveshapes…
There is an additional method—you could simply use microphones to capture the acoustic sound of the Motors! But that's up to you guys to experiment with :)
ET: What is the structure of the signal flow in the Motor Synth like?
IK:
ET: It seems that currently, Motorsynth comes only in the portable desktop version. What happened to the keyboard version? Are you still planning to make a production run of those?
IK: Yes—we really did shoot for the stars with the MOTOR Piano, haha!
When we settled on the Synth/Keyboard Idea then we just kept adding and adding stuff and when we finally realized the level of complexity and the size of the project—30 + electromotors, 10-note polyphony, all analog, and tons of features… I guess we're all kind of hopeless optimists, so we just went: “Hell Yeah! Let's go nuts and make a 21st century Hammond Synth Organ”
We gave it a good shot, and I am really proud of the design that we made for the MOTOR Piano—I think it's much cooler than Tesla's Cybertruck, haha!
What happened was—we sunk about 6 months into the MOTOR Piano and realized that we were not even close to a finished project. Then we showed the prototypes to the engineers and product designers at Moog. They were extremely supportive and helpful and gave us a 3-hour long lecture (at least) about product evolution and design. It was quite perfect timing, because they themselves had just gone through multiple years'-worth of development work for the Moog One, so they illustrated many technical challenges to us that we might face with such a huge instrument.
The main takeaway was—don't try to create the “Masterpiece” straight away: start with smaller formats and perfect all the building blocks, THEN put everything you've learned into the Ultimate Mothership version.
After hearing this story, we re-evaluated the project and decided to change course. That was in late January 2019…by May 2019 we had already completed a full redesign of the Motor concept and presented the first working prototypes of the MOTOR Synth at Superbooth...and we then spent eight more months perfecting the MOTOR Synth and only NOW we finally are happy with it, and we are extremely glad everything worked out this way. The MOTOR Synth development process taught us SO much! At this point we kind of feel that we might be among the world's leading electromotor experts...
So, ultimately, we will definitely develop and produce the big MOTOR Pianos, but I can't tell you when exactly. I'm sure that the MOTOR Synth will have a very passionate fanbase, we would like to collect and analyze user feedback etc. before we barge into a new development project! I guess we're becoming wiser, hahah!
While you wait for the big MOTOR Piano—the MOTOR Synth is packed with features and is also compatible with all MIDI keyboards, so I don't think you'll be getting bored with it anytime soon.
ET: When I first heard about the Motorsynth, I immediately thought of instrument aging? Like, with acoustic, analog or electromechanical instruments time adds to the character of the sound. I wonder how/if the sound of the Motorsynth will change as the motors get older? Did you think about that part as you were designing the instrument?
IK: The type of Motors that we use for the MOTOR Synth are called brushless DC motors. “Brushless” means that there is no physical connection or friction between the Motor's rotor and stator. So, in theory, a Motor like this could be spinning away for thousands and thousands of hours, especially since there is no mechanical load on the Motors bearing. We estimate well over 20,000 hours of continuous operation for each motor, which, according to scientists is enough.
Time will show what sort of longevity the Motors will actually demonstrate, but in any case, the Motors themselves are an easily replaceable part. They are standard drone Motors that can be easily obtained and replaced with a screwdriver.
We're kind of used to this—there was a lot of concern from people regarding the PLASMA tube's longevity as well...so far not one single tube out of thousands has burnt out or caused any issues. The longest-running PLASMA Pedal has been continuously on for over a year-and-a-half now and is showing no signs of wear or damage. I suppose when you do new and strange things there will always be skeptics, as well as a certain element of risk, but that's just how life goes.
Follow the Light...Pedal
ET: What is the process for you of taking an idea and developing it into a finished product? Do you have a paved pathway, or is it different with each product?
IK: The process is always different and to be fair - we don't have that many products yet—so we kind of go case by case. I do like the David Lynch philosophy though, where he compares Catching Ideas to Fishing: “Desire for an idea is like bait on a hook”.
First you need to dream and try to catch a vision, an idea. Then you figure out a way to make that vision a reality.
This is how our newest release LIGHT Pedal was born. Early this summer, one of our engineers Teo (Teodors Kerimovs) started performing seemingly random experiments with lights, sensors, and transducers. For almost a month, it wasn’t fully clear what he was doing, and Teo just said that he’s looking for a way to create reverb from light reflections. We did our best to support him and tried to brainstorm ideas together.
Then one moment the absolutely obvious solution hits you – read a Spring Reverb with IR Sensors! We tried it – it worked! Sounds fantastic! Then you start building...
ET: Can you tell more about the Light Pedal? What is it? How does it work? And when can we expect it to be available?
IK: The LIGHT Pedal is what we call an Optical Spring Reverb System.
In essence - we use IR optical sensors to detect the tiny movements that take place in a spring tank as sound is traveling through it. First of all - the IR sensors themselves are much more sensitive than the Transducer pickups used in traditional Spring Tanks. This allows to harvest extremely delicate movements on the spring's surface, which would otherwise be lost - this adds to the texture and decay length of the Reverb.
Secondly, the IR sensors can be placed at different regions on the spring, which will substantially alter the character of the Reverb sound. For example - if you place an optical pickup in the middle of the spring, where the movement amplitude will be higher than in the spring's ends, you will get a more aggressive, grainy type of reverb sound.
It is quite a fascinating world and we are still fine-tuning the LIGHT Pedal and exploring all the sounds that can be created with this optical system. We showed the pre-production model at Winter NAMM 2020 and received so much positive feedback and even got an Innovation award from MUSIC RADAR, haha!
I'm laughing cause this whole idea started in such an innocent and abstract way - with Teo dreaming about turning Light into Reverb!
Picking the Right Idea
ET: As a brand, you’ve set a pretty high standard for yourself. Always coming up with things that haven’t been done before sounds very liberating on one end, but I can see it also being very stressful, as you have to keep challenging yourself. Do you get anxious about coming up with ideas for future inventions or do you have a stack of ideas that you are just gradually bringing to life one by one?
IK: As I've mentioned in a previous paragraph, we do have a very strict evaluation system for new ideas. Any new idea has to meet the following criteria:
1) It has to be something original and something that's never been done before.
2) It has to have practical value, such as new sounds, interesting tonal quality or some kind of unique character
3) It needs to be exciting and stimulating!
When you play the MOTOR Synth you can hear the motors buzzing in the box and you see the discs spinning it really draws you in and it makes the whole experience just phenomenal. The same goes with the PLASMA Racks—when you're cranking it up, watching audio signal being ripped to shreds by giant electrical probes - you really start to catch a new kind of inspiration; your mind starts going into completely new directions.
We think that all good musical instruments should always be inspiring. That's why I'm so excited for the LIGHT Reverb release—It's a very intimate and inspiring sound device.
Inspirations
ET: What other modern instrument designers are you inspired by? Anyone particular you would like to collaborate with?
IK: Well, I've already mentioned Teenage Engineering—they are a huge inspiration in terms of design and functionality, as well as just Originality. Just take a look at how well-designed their instructions are in their packaging—it's an amazing experience.
I'm really inspired by Girts and Kodek from Erica Synths because they've shown us and everyone in our region that you can do great things here in Riga, in our hometown. All you need is an internet connection and a passion for what you do.
I'm also totally inspired by Jamie and Julie from EarthQuaker Devices, because I think they have built much more than a pedal brand—it is a super friendly, supportive community of players, who share a common approach to music-making, gear, and style. I also think they might be among the first pedal companies to start producing serious educational materials about gear, such as their YouTube series Show Us Your Junk, etc...
In terms of Guitars, I am a life-long fan of Fender (and Gretsch). I think that they sound and play fuckin great and I'll take a 600$ Mexican Tele over some Boutique monstrosity any day of the week.
There is ONE exception though—I recently started researching aluminum instruments, and kind of have fallen in love with them...I've tried out multiple brands, but so far hands-down the best work is by a British “luthier” named Pete Longfellow; the brand is called Longfellow.
He makes incredibly beautiful aluminum guitars, and I love his approach - his main focus is on building a Beautiful Hand-welded Aluminum body. Then he'll take a decent neck, some Fender pickups and a set of decent hardware and simply put it all together. This is the result:
I will be honest with you—I haven't been this happy with any guitar in my life. I have no idea if it sounds better or worse than anything else, but it's just such a joy to play it, it has an original sound, look and feel and, most importantly—it inspires! It isn't even that expensive (under 1.5k), but I still kinda feel spoiled to have it…
ET: We tend to ask a question about impossible project ideas in our interviews. In your case, it seems to be particularly appropriate. Do you have any ideas for a project that you would like to accomplish but it is just impossible to do in this day and age?
IK: Oh yeah, we often have ideas that they're completely crazy and then after a few weeks of late-night reading and brainstorming you just have to admit it to yourself that's “Okay this one is physically impossible.”
That happened this summer—we got really hyped up about building a Delay/Modulation unit based on a certain physical process (sorry—can't tell what it is). After a few months of reading and experimentation we had to admit that the physics simply doesn't work out, but it was a fun learning experience. We really are constantly looking for unexplored territories and once in a while everything lines up perfectly. : )